Chapter 10 Sheet Metal Design is. Flag for inappropriate content.
Design For Manufacturing And Assembly Ppt Video Online Download
When designing a sheet metal.
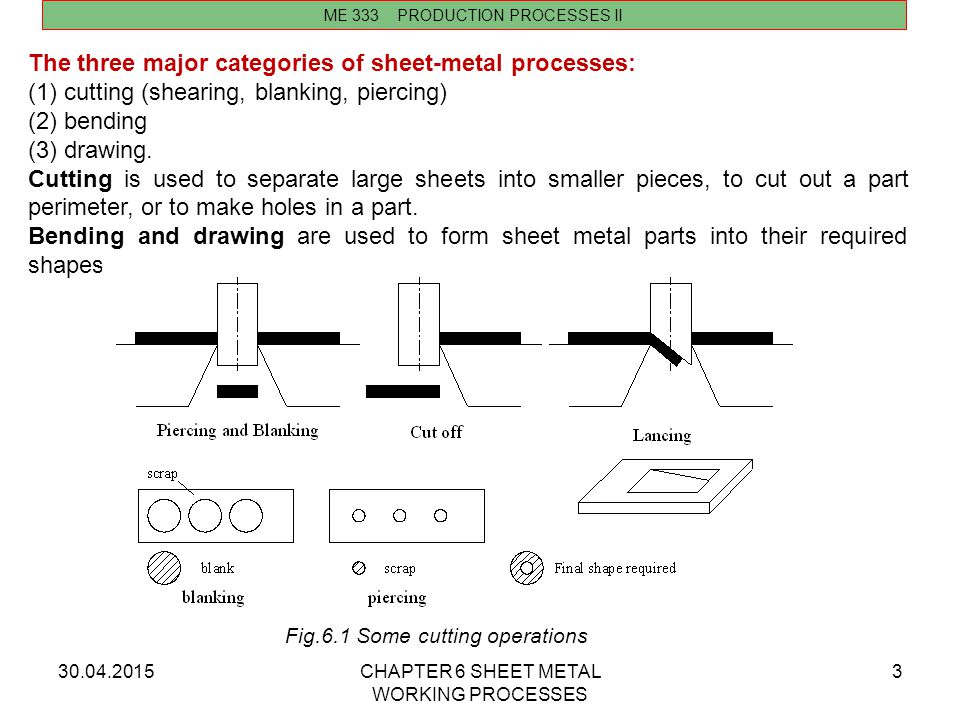
. Brass is strong and the hot versus cold working characteristics can be varied depending on the quantity of zinc in the alloy. We typically use C1100 for sheet metal forming. Following are some basic sheet metal design Thump rules for Sheet metal Design.
Curls dimension outside radius must be at least twice the materials thickness. Basic geometry feature of the dieface Although an actual dieface is a rather complicated system of surfaces some basic. Engineering changes can be costly.
They are all artistically enhanced with visually stunning color shadow and lighting effects. Sheet Metal Basics design guidelines a metal sheet varying in between 0154mm to 635mm. For the ease of manufacturing multiple bends on the same plane should occur in the same direction.
Sheet metal manufacturing is suitable for a range of metal materials. We will dive into the details of these techniques shortly. D 25T R see below The height can be less but it required secondary operations and is far more costly.
Outline Attaching things permanently and temporarily Simple structural supports and enclosures sealing o-rings Designing things that have to move bearings tracks jamming issues Modular solutions MK macrobench dexion Permanent Attachment Welding later Brazing later Rivets Glue Epoxy. With an external style sheet you can change the look of an entire Web site by changing one file. The gel and enzyme are held in place on the surface of the ion selective electrode by an inert physical support.
Continuing our focus on sheet metal forming this issue of DFM guidebook focuses on design guidelines for bend relief parameters distance between holes and bends and offset bend material when a bend is made close to an edge. Attribution Non-Commercial BY-NC Available Formats. Dieface design The simplified die addendum.
Sheet Metal Bending Radius. Sheet Metal Operations Not Performed on Presses 7. Sheet Metal Fabrication - Sheet metal is a kind of integrated metal cold working technology for metal sheet usually in under 6mm usually the parts plastically deformed by handwork or stamping die to form your desired shape and size and it also can be further formed more complex parts by welding or other metal cold working technology including Laser cutting.
These techniques often work in tandem with one another to produce the required part. Many of them are also animated. Ppt On Sheet Metal Process 8 Mistakes To Avoid When Designing Sheet Metal Parts Sheet Metal Working Processes Ppt Download Chapter 10.
Or how to put together simple things simply. 2007 John Wiley Sons Inc. Download as PPT PDF TXT or read online from Scribd.
Form height to thickness ratio To determine the minimum form height for sheet metal use the following formula. Save Save Presentation on Press Tool Design 01 For Later. All other factors influencing sheet metal forming we should recall that a sheet metal forming operation can always be from the conceptual point of view.
Ppt on Sheet metal process 1. Sharp inside bend radius in sheetmetal parts can cause material flow problems in soft material and fracturing in hard material. Usually made by hammering or rolling Trending Topics by Ak.
When Sheet metal parts have sharp corners try designing a fillet half of the material thickness. Sheet Metal Design Basics Ppt - Tool And Die Design For Sheet Metal Solidworks Youtube Access google sheets with a free google account. A great practice here is to ensure that the minimum bend radius for mild steel sheet metal is equal to its thickness.
G India Business Center Part Design Guidelines Sheet Metal Part Design Guidelines. Enter 5mm in the Default Bend Radius field. Click the Sheet Metal Parameters icon.
If you design sheet metal parts you may know that bend relief is a notch cut made into the. Bends in sheet metal are manufactured using sheet metal brakes. Tabs must be at least 2 times the sheets metal thickness or 0126 32mm whichever is greater and can be no longer than 5 times its width.
-9- Stamping Basics Involve us during design stage to optimize cost and performance in component design. The PowerPoint PPT presentation. The basic sheet metal fabrication techniques include cutting bending punching stamping welding and finishing.
Sheet metal parts with a minimum of 09mm to 20mm in thickness can be manufactured. The Sheet Metal Parameters dialog box is displayed. Select the Bend Extremities tab.
M P Groover Fundamentals of Modern Manufacturing 3e SHEET METALWORKING 1. While stamping offers precision and good reproducibility consideration must be given to the amortization. F YS UTS2 A.
For hard materials Stainless steel CRCA an inside bend radius equal to 065 times of sheet thickness is also enough. A - 1 degree tolerance on all bend angles. Defining the Sheet Metal Parameters This task shows you how to configure the sheet metal parameters.
Stress distribution through the thickness of the part. Avoid large sheet metal parts with small bent flanges. COPPER An alloy of copper and zinc brass is very ductile and corrosion resistant.
The minimum sheet metal bend radius depends on the manufacturing process and tool used. Minimum Practical Section should never be less than material thickness or 060. A minimum section must be one and one half times material thickness for high shear strength material for the most practical stamping.
Our new CrystalGraphics Chart and Diagram Slides for PowerPoint is a collection of over 1000 impressively designed data-driven chart and editable diagram s guaranteed to impress any audience. The more flexible the metal the easier it is to attain a small inner bend radius. Dies and Presses for Sheet Metal Processes 6.
When designing parts for laser cutting one should not make holes smaller than the thickness of the material. Enter 1mm in the Thickness field. 84 32 84 found.
Recommended inside bend radius for sheet metal parts should be equal to material thickness. F stretch forming force lbs YS material yield strength psi UTS ultimate tensile strength of the material psi A Cross-sectional area of the workpiece in2 Forces needed to bend sheet metal. This gives brass sheet a wider range of performance depending on end use of the designed part.
Other Sheet Metal Forming Operations 5.
Sheet Metal Design Guidelines How To Design Good Sheet Metal Parts
Chapter 10 Sheet Metal Design Ppt Download
Chapter 10 Sheet Metal Design Ppt Download
Chapter 10 Sheet Metal Design Ppt Download
Ppt Chapter 10 Sheet Metal Design Powerpoint Presentation Free Download Id 6655822
Ppt Chapter 10 Sheet Metal Design Powerpoint Presentation Free Download Id 6655822
0 comments
Post a Comment